Material Matters: The Carbon Fiber Revolution

June 3, 2020
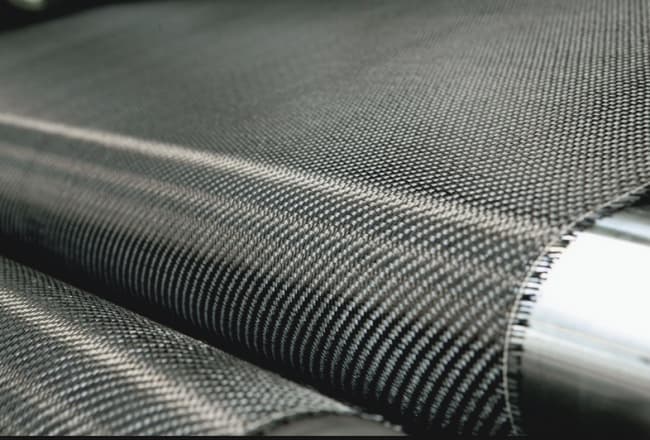
For over half a century, we’ve been manufacturing the highest quality workplace safety equipment from Englewood, Colorado.
We believe that making extraordinary equipment requires extraordinary care. That care extends throughout our design and manufacturing process. It starts all the way with the selection of the best materials to make our products.
Every aspect of our products makes a difference. With that in mind, we want to use this space to take a closer look at the materials we choose to ensure our products perform and protect at the highest standards.
Last time out, we did an in-depth examination of the fabric we use for our work tents.
Today, we’re examining one of the key components of one of our most innovative fall prevention tools: the Uni-Lite Fall Arrest Post. And the material that sets it apart from the rest is one that we’re becoming increasingly familiar with in our day-to-day lives: carbon fiber.
Properties
When looking in-depth at materials, one phrase that comes up again and again is “strength-to-weight ratio.” Also called a material’s “specific strength,” this measures the strength of a substance as divided by its density.
A material’s strength is defined as the force applied at a given unit area—i.e., Newtons per square meter—at the point of failure for that specific substance.
Or, in words any five-year-old playing with their toys intrinsically understands, “how hard can I mash this thing before it breaks?”
Specific strength, as we’re using it here, is measured in kilonewton meters per kilogram. Currently, there’s no standard SI-approved unit to measure specific strength.
A material like concrete has a very low strength-to-weight ratio (5.22 kNm/kg), but since loads on concrete are generally well-distributed, it’s well-suited for the job (drop a bowling ball on some concrete though, and you’ll see some breakage). Titanium clocks in with a ratio of 76 kNm/kg, and aluminum alloy reaches 116 kNm/kg.
Carbon fiber has an eye-popping strength-to-weight ratio of 3,911 kNm/kg. Note, there are a variety of carbon fiber blends, weaves, and precursors, all of which has an effect on the final product. This number is meant as a ballpark. Even still, when compared to titanium, we get a clear impression of the advantage of carbon fiber.
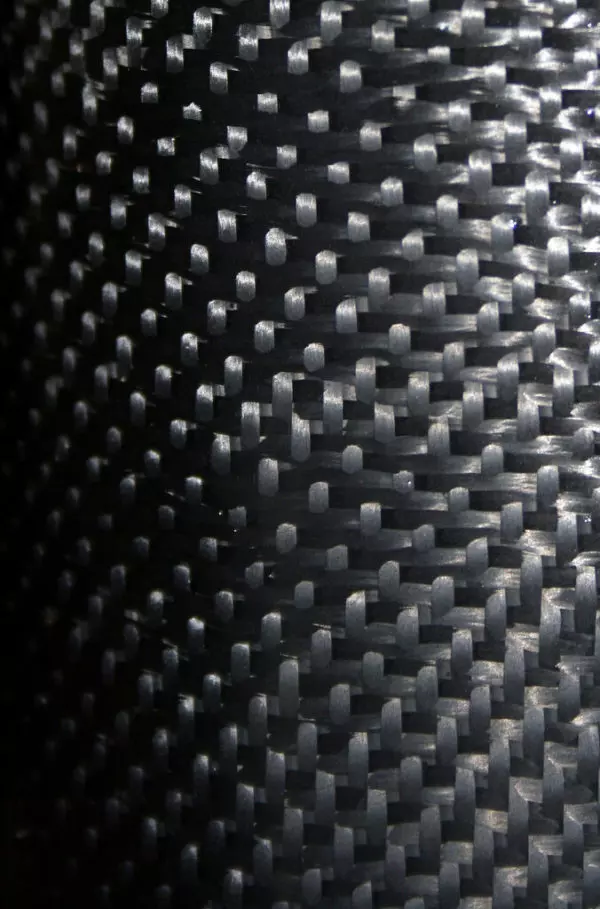
An individual fiber is thinner than a human hair, but strong along its length. These fibers are bound together like rope and then woven into a fabric to give it incredible strength.
In its untreated state, carbon fiber is strong, but stiff and brittle. To be usable, carbon fiber is treated with different resins suited for different applications. These resins add crucial flexibility which allow the carbon fiber to withstand heavy loads.
History
While we associate carbon fiber technology with the advancements of the present day, it actually dates back to the invention of the lightbulb.
Carbon fiber was first invented by Joseph Swan in 1860 for use as lightbulb filament. In 1879, Thomas Edison baked bamboo slivers and cotton threads at high temperatures, thus carbonizing them. As the 19th century went on, carbon fiber technology became more and more reliable for use in incandescent lighting. However, at the time, these fibers were not quite suitable for other applications.
In the late 1950s, a Union Carbide employee named Roger Bacon began carbonizing rayon. These fibers were an improvement, but still brittle, and only about 20% carbon. In the early 60’s, Dr. Akio Shindo led the development of a carbonization process using polyacrylonitrile (PAN) as a base material.
Nowadays, PAN is the most commonly used raw material for making carbon fiber, although the process using rayon as a base has improved to the point where it produces consistently high-quality carbon fibers.
The US Department of Energy’s Oak Ridge National Laboratory has a program that manufactures PAN-based carbon fiber and distributes it for testing.
How We Use It
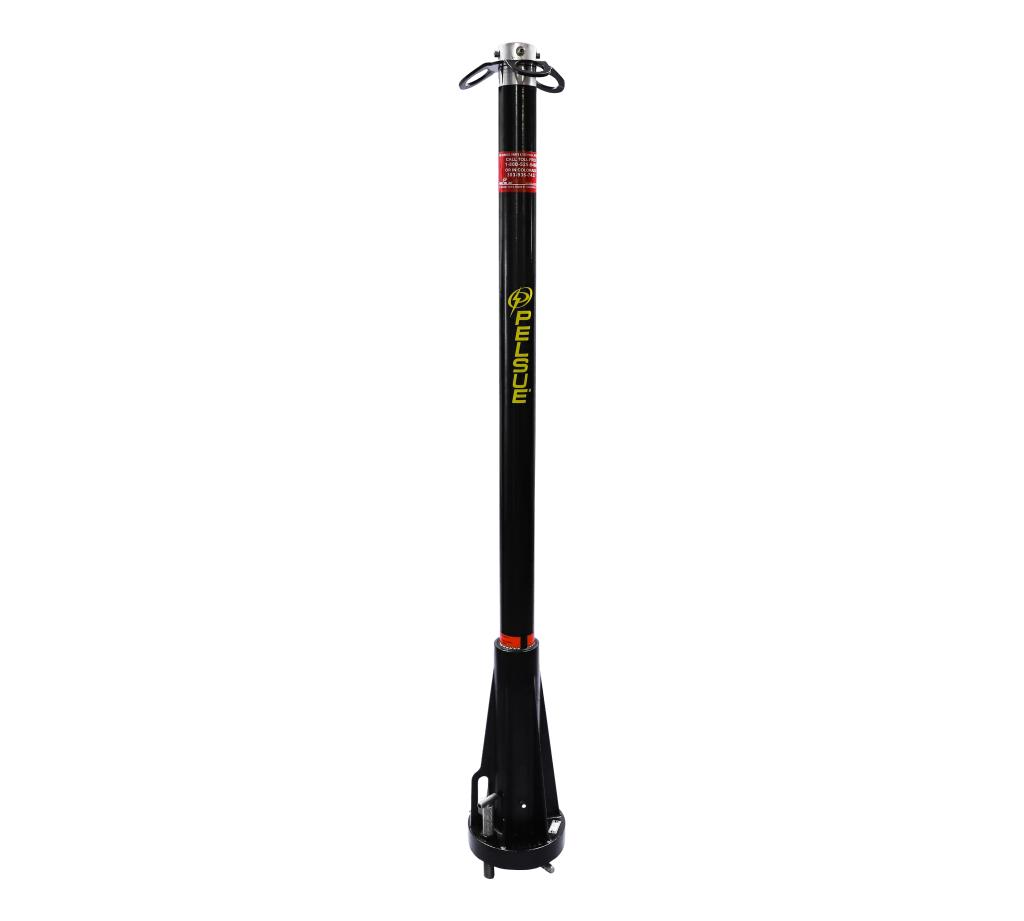
The use of carbon fiber gives our Uni-Lite Fall Arrest Post unbeatable strength while minimizing the weight of the unit.
More than strength, the Uni-Lite is remarkable for its flexibility. This means that should a worker fall while attached to the Uni-Lite, it bends to absorb the force of the fall, which helps arrest the worker’s momentum while minimizing the force exerted on the worker.
The carbon fiber post is combined with aluminum and plastic components to create the anchors and tie-offs needed to support up to three workers from an elevated point.
In our long history of innovation, we’ve found and used new materials to manufacture products that save lives. The Uni-Lite is one of the latest and greatest examples of this, and its high functionality is due in no small part to carbon fiber technology.